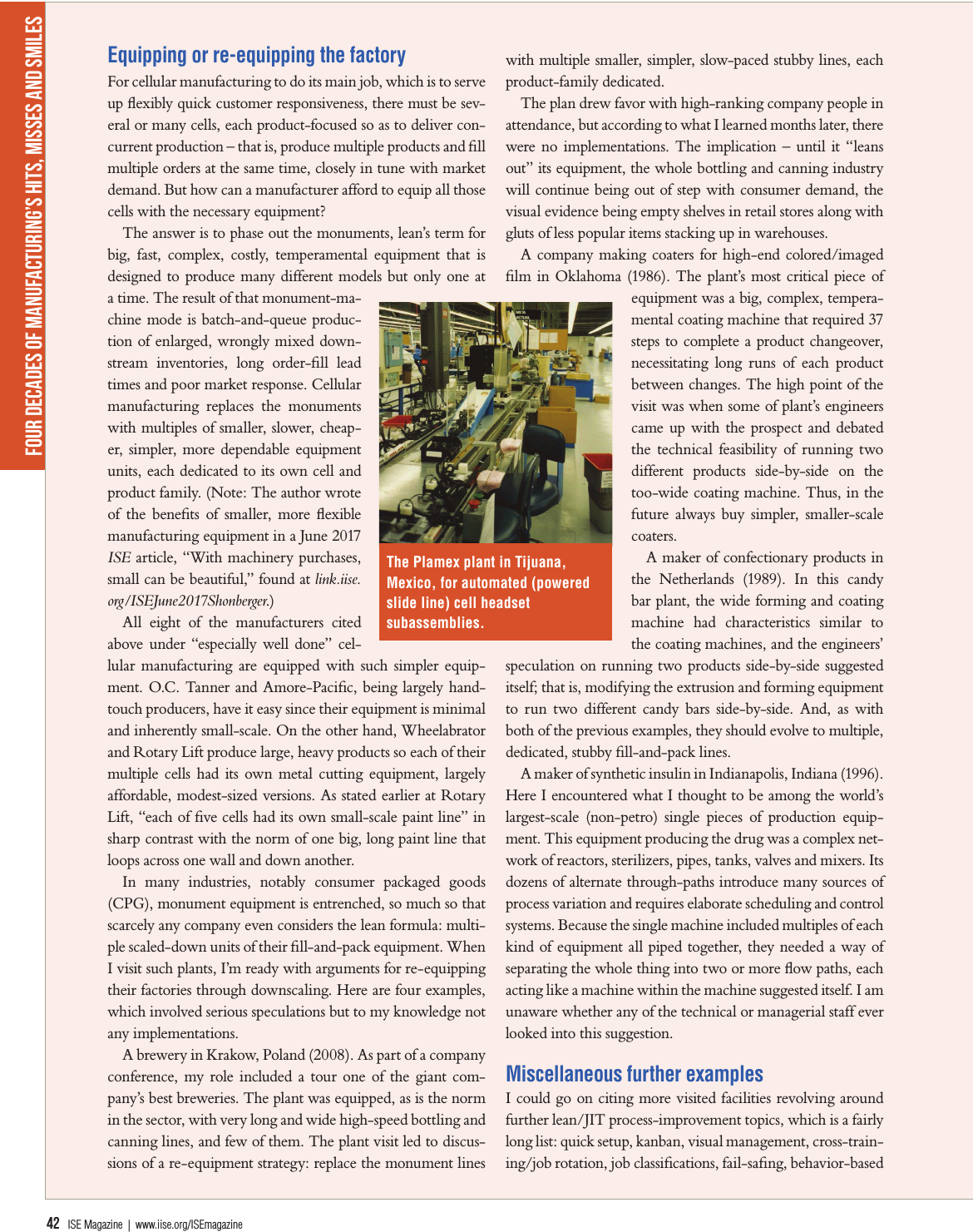
42 ISE Magazine | www.iise.org/ISEmagazine
Equipping or re-equipping the factory
For cellular manufacturing to do its main job, which is to serve
up flexibly quick customer responsiveness, there must be sev-
eral or many cells, each product-focused so as to deliver con-
current production – that is, produce multiple products and fill
multiple orders at the same time, closely in tune with market
demand. But how can a manufacturer afford to equip all those
cells with the necessary equipment?
The answer is to phase out the monuments, lean’s term for
big, fast, complex, costly, temperamental equipment that is
designed to produce many different models but only one at
a time. The result of that monument-ma-
chine mode is batch-and-queue produc-
tion of enlarged, wrongly mixed down-
stream inventories, long order-fill lead
times and poor market response. Cellular
manufacturing replaces the monuments
with multiples of smaller, slower, cheap-
er, simpler, more dependable equipment
units, each dedicated to its own cell and
product family. (Note: The author wrote
of the benefits of smaller, more flexible
manufacturing equipment in a June 2017
ISE article, “With machinery purchases,
small can be beautiful,” found at link.iise.
org/ISEJune2017Shonberger.)
All eight of the manufacturers cited
above under “especially well done” cel-
lular manufacturing are equipped with such simpler equip-
ment. O.C. Tanner and Amore-Pacific, being largely hand-
touch producers, have it easy since their equipment is minimal
and inherently small-scale. On the other hand, Wheelabrator
and Rotary Lift produce large, heavy products so each of their
multiple cells had its own metal cutting equipment, largely
affordable, modest-sized versions. As stated earlier at Rotary
Lift, “each of five cells had its own small-scale paint line” in
sharp contrast with the norm of one big, long paint line that
loops across one wall and down another.
In many industries, notably consumer packaged goods
(CPG), monument equipment is entrenched, so much so that
scarcely any company even considers the lean formula: multi-
ple scaled-down units of their fill-and-pack equipment. When
I visit such plants, I’m ready with arguments for re-equipping
their factories through downscaling. Here are four examples,
which involved serious speculations but to my knowledge not
any implementations.
A brewery in Krakow, Poland (2008). As part of a company
conference, my role included a tour one of the giant com-
pany’s best breweries. The plant was equipped, as is the norm
in the sector, with very long and wide high-speed bottling and
canning lines, and few of them. The plant visit led to discus-
sions of a re-equipment strategy: replace the monument lines
with multiple smaller, simpler, slow-paced stubby lines, each
product-family dedicated.
The plan drew favor with high-ranking company people in
attendance, but according to what I learned months later, there
were no implementations. The implication – until it “leans
out” its equipment, the whole bottling and canning industry
will continue being out of step with consumer demand, the
visual evidence being empty shelves in retail stores along with
gluts of less popular items stacking up in warehouses.
A company making coaters for high-end colored/imaged
film in Oklahoma (1986). The plant’s most critical piece of
equipment was a big, complex, tempera-
mental coating machine that required 37
steps to complete a product changeover,
necessitating long runs of each product
between changes. The high point of the
visit was when some of plant’s engineers
came up with the prospect and debated
the technical feasibility of running two
different products side-by-side on the
too-wide coating machine. Thus, in the
future always buy simpler, smaller-scale
coaters.
A maker of confectionary products in
the Netherlands (1989). In this candy
bar plant, the wide forming and coating
machine had characteristics similar to
the coating machines, and the engineers’
speculation on running two products side-by-side suggested
itself; that is, modifying the extrusion and forming equipment
to run two different candy bars side-by-side. And, as with
both of the previous examples, they should evolve to multiple,
dedicated, stubby fill-and-pack lines.
A maker of synthetic insulin in Indianapolis, Indiana (1996).
Here I encountered what I thought to be among the world’s
largest-scale (non-petro) single pieces of production equip-
ment. This equipment producing the drug was a complex net-
work of reactors, sterilizers, pipes, tanks, valves and mixers. Its
dozens of alternate through-paths introduce many sources of
process variation and requires elaborate scheduling and control
systems. Because the single machine included multiples of each
kind of equipment all piped together, they needed a way of
separating the whole thing into two or more flow paths, each
acting like a machine within the machine suggested itself. I am
unaware whether any of the technical or managerial staff ever
looked into this suggestion.
Miscellaneous further examples
I could go on citing more visited facilities revolving around
further lean/JIT process-improvement topics, which is a fairly
long list: quick setup, kanban, visual management, cross-train-
ing/job rotation, job classifications, fail-safing, behavior-based
The Plamex plant in Tijuana,
Mexico, for automated (powered
slide line) cell headset
subassemblies.
Four decades of manufacturing’s hits, misses and smiles